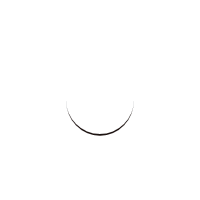
Cart
CloseNo products in the shopping cart.
No products in the shopping cart.
DAVE Embedded Systems has a huge experience in coating and sealing of embedded systems for many applications. Railways, transportation and military/avionics are the main areas where these features are required but also many industrial products requires to protect the electronics boards against:
DAVE Embedded Systems has developed its own internal quality procedures in according with the standards MIL 610 and 610D. In the following are described the main working phases with some hints about our internal quality procedure:
Before apply any sealing or coating it is important to clean the board even if a noclean paste is used. Typically we adopt a Co-solvent product like TOPKLEAN EL20-R. A
The main scope of Sealing is to preserve BGA by DUST or DIRTY that can cause failure on the field. Sealing product must be easily removed in case of service repair, since a peel mask product must be used. We adopt typically approved sealing material for military applications likeDYMAX 9-20318-F which requires UV Curing. With this material a good result is assured in automatic process with great repeatibility. In particular bubbles and void are easily solved with this kind of process and material.
After the sealing process it is possible to proceed with conformal coating process. Typically this process should require to protect some areas from coating application. For this reason masking is mandatory.
Masking operation is need to:
Preserve area required to be clear by coating
Mask mechanical holes to prevent that coat cross PCB to one side to other side during coating (coating defect issues can happen)
Masking operation can be performed with adhesive tape material on mechanical holes and on top of components and with other type of peel masking.
The main scope of Coating is to preserve components from dirty and external agents (humidity, etc..) that can cause failure on the field. Coating product must be easily removed in case of service repair, since a peel mask product must be used Humiseal 1B73 with a variable thickness min 25um - max 75um.
Welcome to the DAVE Embedded Systems' technical information form submission portal!
Please fill in the fields below. The support team will take care of you in maximum 24h!
Welcome to the DAVE Embedded Systems' Documentation system. Please fill in with required information and you will get your document! Thank you!.
We use cookies to personalize content, to get traffic statistics and to improve your experience on our website.
Please read our Cookie Policy for a more detailed description and click on the "Manage preferences" button to customize how the site uses cookies for you. By clicking on "Accept all cookies" you give your consent for the use of each type of cookie.
These cookies are necessary for the website to function and cannot be switched off in our systems.
You can set your browser to block or alert you about these cookies, but some parts of the site will not then work. These cookies do not store any personally identifiable information.
These cookies allow us to count visits and traffic sources so we can measure and improve the performance of our site. They help us to know which pages are the most and least popular and see how visitors move around the site.
All information these cookies collect is aggregated and therefore anonymous. If you do not allow these cookies we will not know when you have visited our site, and will not be able to monitor its performance.
Select all Deselect all